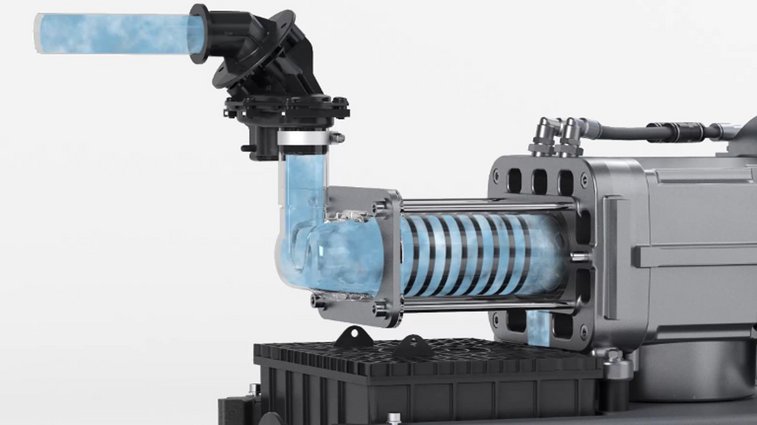
Vacuum generation in screw pumps is based on gas transport in gap-sealed chambers.
Screw pumps have established themselves for vacuum generation in addition to other areas of application. Their design enables the generation of deep vacuum without contaminating processes with oil or abrasion. New advanced screw pump technologies even meet additional requirements such as high chemical resistance and high condensate compatibility for use in laboratories.
Vacuum technology has become an indispensable part of today's research and analysis laboratories. Numerous processes such as filtration, evaporation or drying can only be carried out efficiently and gently with vacuum as an important aid. Specific requirements for vacuum equipment are determined by the application. What does that mean in concrete terms?
The continuous trend towards high product purity and clean process control results in increased demands on applications in the laboratory. In these cases, oil-free and dry pump technologies contribute to contamination-free operation. They do not require operating fluids (e.g. for sealing) that could enter the process. In addition, they improve efficiency and sustainability by eliminating maintenance-related oil changes and emissions, as well as waste oil disposal. For processes involving aggressive gases and vapors, high chemical resistance is also a basic requirement. For these cases, additional chemically resistant pump technologies are required to ensure smooth and durable operation.
Which vacuum pumps meet these two requirements – oil-free operation and chemical resistance? Dry chemistry diaphragm pumps have been established in laboratories since the 1980s. They enable vacuum down to approx. 1 mbar, which is, however, not sufficient for all processes. For even deeper, clean vacuum, there are dry screw vacuum pumps, or screw pumps for short. These are also suitable for process pressures down to the 10-3 mbar deep fine vacuum range. For a long time, however, the original industrial pumps were not available for laboratory scale or in a particularly chemically resistant design. The solution: Today, newer developments in screw pumps allow the adapted use of this vacuum technology in the laboratory as well.
Functionality of the screw pump
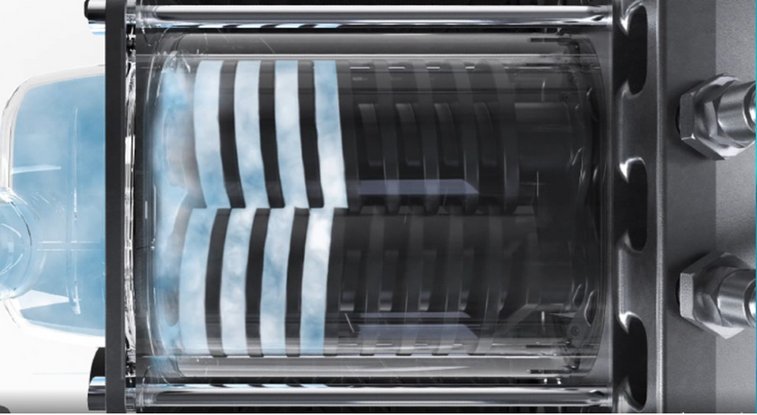
View from above: Counter-rotating spindles transport the trapped gas volume to the outlet of the screw pump.
Screw pumps for vacuum generation belong to the group of dry-running pumps and operate according to the rotating displacement principle, as do, for example, roots pumps. The origin of this principle is the Archimedean screw, originally a water lifting device of antiquity with a rotating screw as the transport and lifting unit. Today's screw pumps for vacuum generation transport gas instead of water and inside them are two rotating displacers or rotors instead of a screw. That is why the screw pump belongs to the two-shaft rotary displacement pumps. Due to their appearance, these rotors are called screws, spirals or spindles.
The vacuum generation of screw pumps is based on gas transport in gap-sealed chambers: The two rotating spindles intermesh without contact and, together with the enclosing stator, form several chambers. Their very narrow gaps are in the micrometer range. While the spindles rotate synchronously in opposite directions, the chambers transport the gas: A mass flow is created along the spindle axis from the inlet on the suction side to the outlet on the pressure side. Due to the heat generated in this process, screw pumps require temperature control by means of cooling liquid or cooling air so that the gap dimensions do not change. This is because the possible ultimate vacuum is mainly determined by both the gap dimensions in the warm operating state and fluid mechanical properties. The pumping speed, on the other hand, is determined among other things by the size of the spindles and their rotational speed, which in turn determines the general dimension of the pump. The following applies: The greater the required pumping speed, the larger the pump.
General advantages of screw pumps
Dry screw pumps for vacuum generation are already widespread in sectors such as chemistry, pharmaceuticals or semiconductor manufacturing. The absence of oil is a major advantage. In addition, screw pumps are versatile due to the variability in vacuum pressure and wide range of pumping speeds. Depending on the pump model, the vacuum pressure varies between ambient pressure and 10-3 mbar. This is why screw pumps are available for applications in both rough vacuum (down to 1 mbar) and fine vacuum (down to 10-3 mbar). In addition, they are suitable as backing pumps for turbomolecular pumps and for other applications with regard to high and ultra-high vacuum technology. The pumping speed of screw pumps ranges from several m³/h to several thousand m³/h, depending on the application.
Screw pumps are also characterized by their low maintenance requirements. The spindles intermesh without contact, which prevents abrasion and wear from occurring in the first place. They also contain no seals in the working chamber that could wear out. In addition, screw pumps do not require any operating fluids such as oil in the working chamber.
In addition, there are other different features, such as the pitch of the spindles, which allows the operating behavior to be adapted to the desired task. If all chambers are the same size, this is referred to as a constant-pitch pump. In variants with variable pitch, the chamber sizes decreases towards the outlet, resulting in compression. Variable-pitch screw pumps do improve thermodynamic properties; there is less heat and noise generation. However, constant-pitch screw pumps have a higher condensate tolerance, which is advantageous for processes involving solvents.
Advanced screw pump from VACUUBRAND
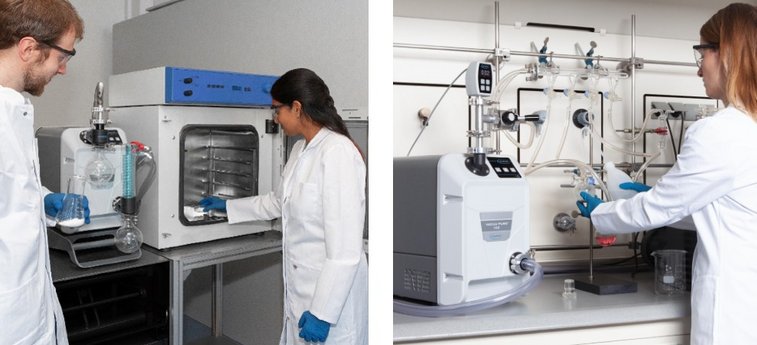
Absolutely oil-free screw pump VACUU·PURE® with high chemical resistance and condensate compatibility
With the new screw pump from VACUUBRAND, it has been possible to further supplement the general advantages of this versatile pump technology with targeted design enhancements specifically for use in the laboratory. The dry screw pump VACUU·PURE® 10C is designed for applications and processes that require chemically resistant, condensate-compatible and absolutely oil-free vacuum pumps:
- Vacuum drying
- Distillation
- Heat treatment
- Schlenk line
- Freeze drying
- Degassing
- Coating
- and many more
High chemical resistance: To ensure that the newly designed VACUU·PURE 10C screw pump is particularly robust against aggressive gases and vapors, we mainly use chemically resistant plastics. These have excellent resistance to most chemicals. They protect the highly vulnerable parts such as the spindles and stator inside the pump, which are in direct contact with the pumped chemicals. It is crucial that these are not just thin coatings, but thick-walled jackets with robust PEEK plastic. In many cases, this eliminates the need for a cold trap to protect the screw pump.
High condensate compatibility: When developing the VACUU·PURE screw pump, we opted for a constant pitch of the spindles. This leads to a high condensate compatibility, for example when using solvents. An integrated regeneration mode also allows the vacuum pump to dry quickly after the end of the process, which increases sample throughput.
100% oil-free: For absolutely clean processes and pure products, we have designed VACUU·PURE with cantilevered spindles and magnetic gears. Due to the cantilevered bearing, while at the same time the spindles are aligned with high precision, supporting bearings in the working chamber are not necessary – and thus no lubricants that could otherwise enter the vacuum process. The magnetic gear also avoids oil lubrication, thus ruling out undesirable reactions with process media or back diffusion into the working chamber.
Another advantage of the new VACUU·PURE screw pump is its air-cooling system, which eliminates the need for a cooling water connection and thus provides additional flexibility at the point of use.
Product variant for non-corrosive processes:
The dry and abrasion-free VACUU·PURE® 10 screw pump focuses on particle- and hydrocarbon-free vacuum. With this property, the screw pump covers further areas of application:
- Analytical applications
- Fore vacuum generation for turbomolecular pumps
- Regeneration of cryo pumps
- and many more