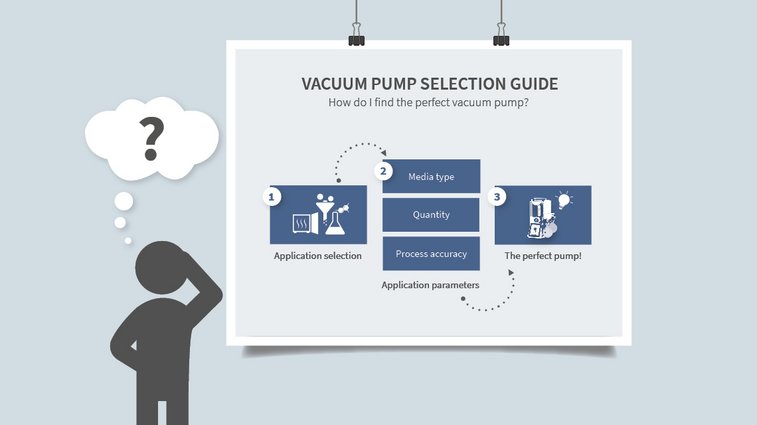
The Vacuum Pump Selection Guide helps to choose the right vacuum pump.
There is a vacuum pump that is best-suited to the needs of every laboratory. But how do users find the right one for their diverse applications? The Vacuum Pump Selection Guide helps them to choose the perfect pump:
Rough or fine vacuum, pumping speed, chemical-resistant version or not, electronically controlled? For some users, these terms used by manufacturers of vacuum pumps don’t mean very much. For the user, the questions are quite different. Which media, such as solvents or buffer systems, do I use? In which volumes? How precisely do I have to work, and how much do I have to regulate the vacuum? Are there further application-specific requirements such as solvent recovery, economic efficiency or explosion protection to consider? We examine the selection criteria in relation to the user's needs and translate manufacturer's technical jargon to help find the right vacuum pump.
For which laboratory application do I need a vacuum pump?
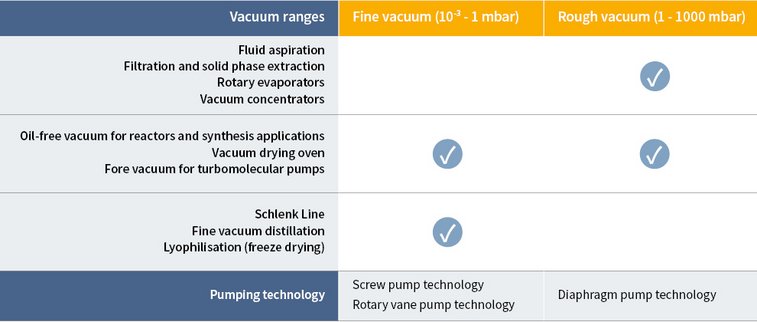
Vacuum ranges and technologies
Filtration, evaporation, drying, concentration and more: vacuum pumps are an important tool for processes like these in labs, pilot plants, and in manufacturing. The type of application determines which pump technology is suitable: a diaphragm pump, rotary vane pump or a screw pump. If the applications take place at a vacuum level of over 1 mbar, pump manufacturers speak of rough vacuum. In this range, diaphragm pumps are an excellent choice. They cover the rough vacuum, run oil-free, and provide users with reliable, low-maintenance vacuum. Some typical applications are
- Fluid aspiration
- Filtration and solid phase extraction
- Rotary evaporators
- Vacuum concentrators
- Oil-free vacuum for reactors and synthesis applications
- Vacuum drying oven (main drying)
The situation is different for applications that require a vacuum level between 1 mbar to 10-3. This range is referred to as the fine vacuum range. Here, either oil-sealed rotary vane pumps or oil-free screw pumps can be used. This range includes applications such as:
- Schlenk Line
- Fine vacuum distillation
- Lyophilisation (freeze drying)
- Oil-free vacuum for reactors and synthesis applications
- Vacuum drying oven (main and residual drying)
Which media do I use?
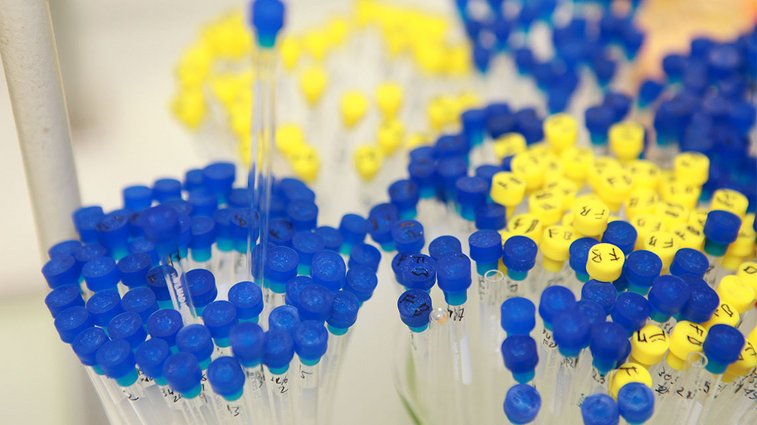
Pump technology depending on the materials used
In laboratories a wide variety of solvents, buffer systems, and other substances are used. Manufacturers of vacuum technology use generic terms such as media or substances. Depending on which media are used in an application, a special type of vacuum pump should be chosen.
If a user works in the rough vacuum range, e.g. filtering samples that contain harmless substances, he is usually well-served with a diaphragm pump in which the parts in contact with the medium are made of aluminium. However, if he uses aggressive media, a special chemistry-rated diaphragm pump with chemically resistant fluoropolymers is required.
In the fine vacuum range, an oil-sealed rotary vane pump can be used. If aggressive media are also to be pumped, a chemistry-HYBRID pump offers significant advantages – a corrosion-optimized combination of a rotary vane pump and a chemistry diaphragm pump. For oil-free operation at low pressures, dry screw pumps are a very good alternative, available in both chemical-resistant and non-chemical-resistant versions.
What volumes do I work with?
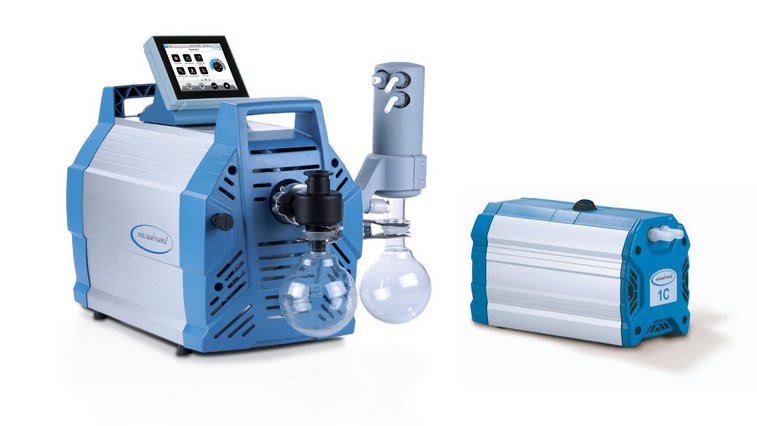
Different sizes and pumping speeds of vacuum pumps
When choosing the right pump, it is also a question of the volumes of solvents used. This is why manufacturer's ask what pumping speed or pumping capacity is needed. The determining factor is, how big is the application: are we still on a laboratory scale or are we in a kilolab or pilot plant operation?
The higher the pumping speed, the faster the pump can evacuate a given volume. The pumping speed specification given by most vacuum technology suppliers is merely the maximum value flow the pump can provide. Usually, this maximum pumping speed occurs at or near normal atmospheric pressure, and generally does not say anything about the effective performance at actual process pressures. It is therefore essential that the user takes a look at the pumping speed curve, which shows how powerful the pump is in the range of the desired process vacuum.
How precise must I be able to work?
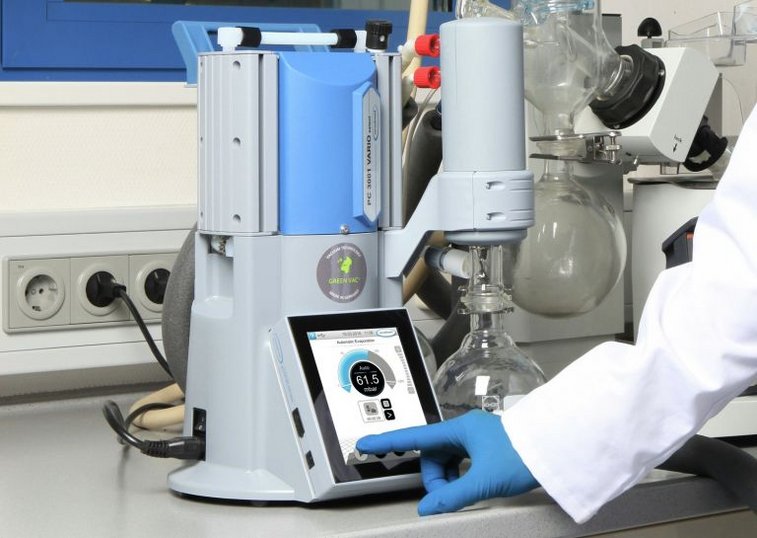
Electronic boiling point detection and vapour pressure tracking for VARIO® pumping systems
Finally, the choice of pump model also depends on the vacuum control requirements. For some applications, such as vacuum drying ovens or filtration, vacuum control is not absolutely necessary. For other applications, however, vacuum control is required.
Diaphragm pumps with electronic VARIO® control are used in the rough vacuum range. These enable precise vacuum control thanks to pump speeds that can be adjusted to suit the requirements. In rotary evaporation, they also automatically detect the boiling point and react to changes thanks to a unique vapour pressure tracking system. VARIO-controlled pumps respond intelligently to changes within the sample vessel and enable optimum process control. For applications in fine vacuum, VACUUBRAND offers various control packages consisting of vacuum controller and suction line valve.
Who can help me choose a pump?
The Vacuum Pump Selection Guide will help you to find the right pump for your application. It covers vacuum solutions for bench-top research up to kilo-lab scale. By answering some simple questions, you will be guided step by step to the best pump solution for your application.
In other cases, there are a variety of complex considerations to account for – such as biological safety standards, ATEX explosion protection or how to supply several work stations through local vacuum networks. If any of these situations applies to you, or you would prefer to discuss your process conditions live, we will be pleased to review your requirements with you.