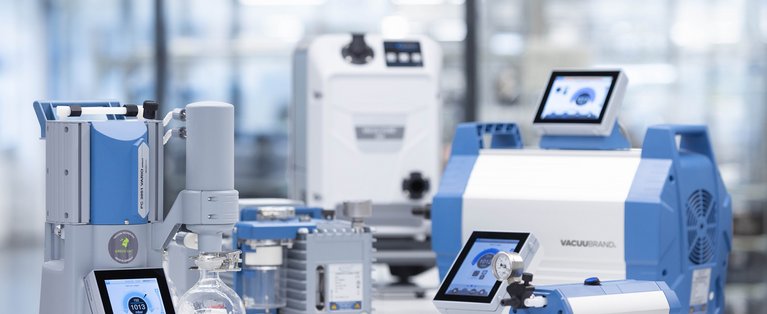
Vacuum pumps
Our vacuum technology enables our customers in the fields of biopharma, chemistry, analytics, physics and renewable energies to run reliable, safe and efficient processes.
Vacuum Pump
Selection Guide
Do you have any
questions?
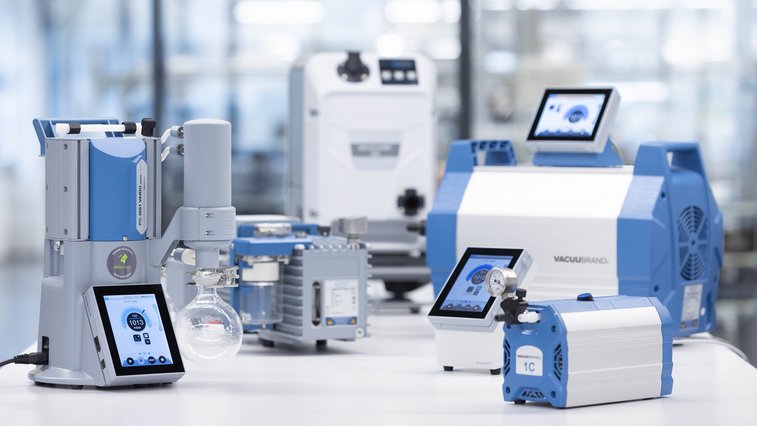
We create the most trusted and
truly innovative vacuum technology,
enabling our customers to create a better tomorrow.
With our vacuum pumps, we have been at the forefront of durability and efficiency for decades. The majority of our pumps do not require operating fluids such as oil or water. This allows us to avoid costs, reduce waste and improve working conditions where our products are used.
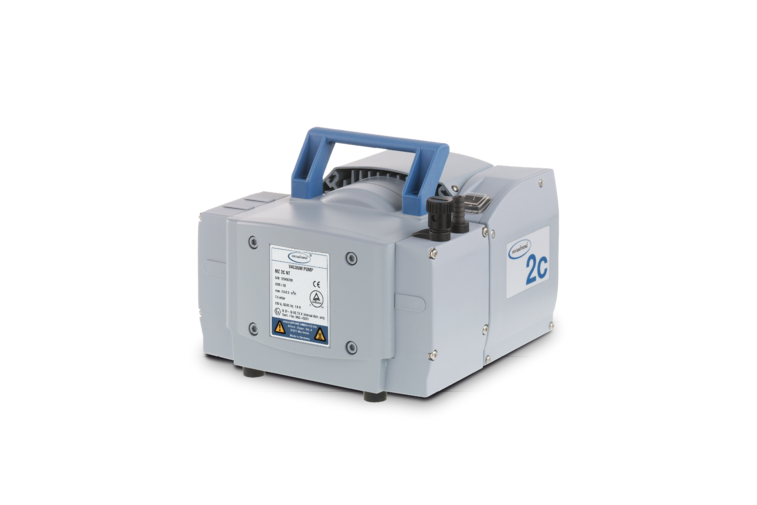
Diaphragm pumps
Diaphragm pumps from VACUUBRAND are the ideal vacuum technology for many laboratory and industrial applications in the pressure range down to 1 mbar. Important advantages include oil-free operation, smooth running, low maintenance and a very long service life.
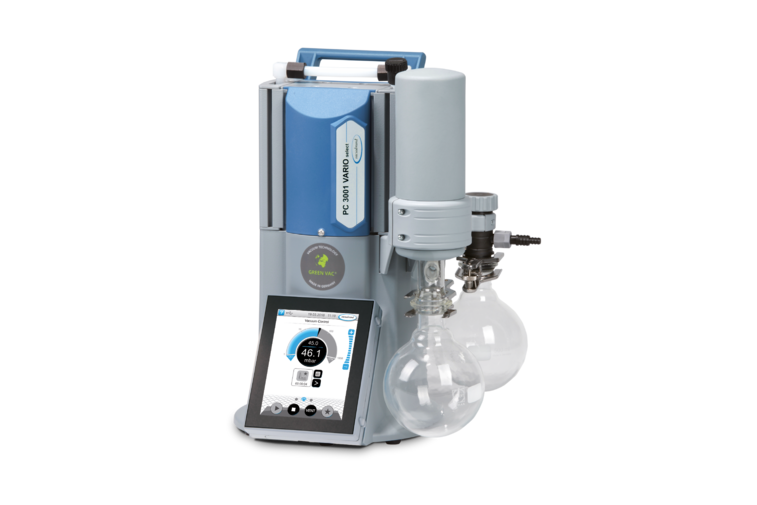
VARIO® diaphragm pumps
Precise, efficient and quiet – VARIO® diaphragm pumps control the vacuum according to need via the motor speed. In combination with the VACUU·SELECT® controller, they achieve the optimal conditions for reproducible processes. The corresponding interfaces enable integration in modern laboratory networks.
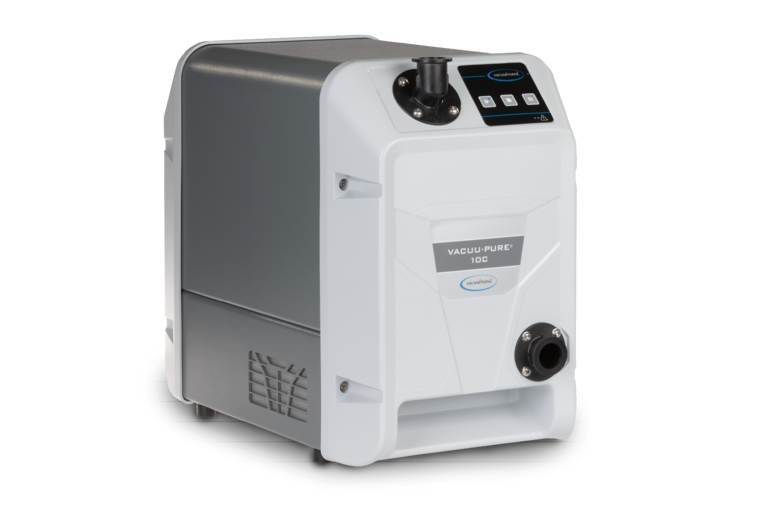
Screw pumps
The VACUU·PURE® dry screw pump is ideal for clean processes in the pressure range down to 10-3 mbar. The screw pump is 100% oil-free, generates no abrasion and has no wear parts. VACUU·PURE 10C is chemically resistant against aggressive media.
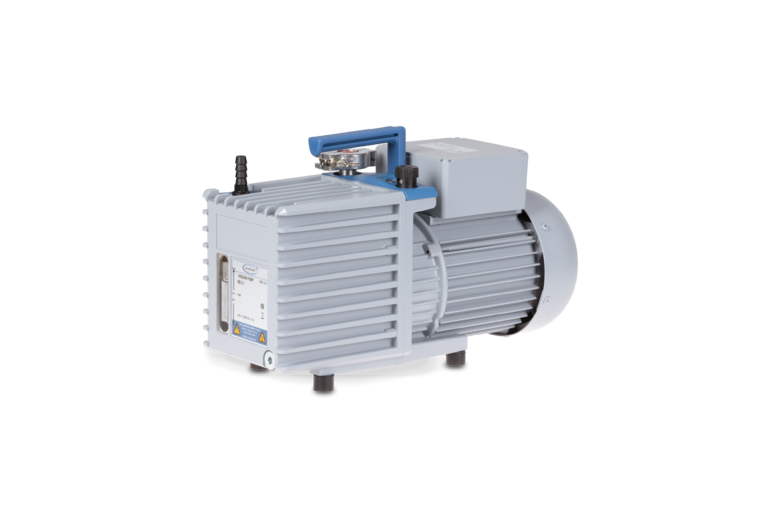
Rotary vane pumps
Powerful and compact - these are our rotary vane pumps for a process vacuum of down to 10-3 mbar. They are designed for use in chemistry and physics, e.g. for lyophilization, Schlenk Line or as a backing pump.
Vacuum Pump
Selection Guide
Do you have any
questions?
Downloads
FAQ
The vacuum requirements always depend on the individual application and the use of different substances such as solvents or buffer systems. Fundamental questions are:
- For which application do I need vacuum technology?
- Which substances do I use?
- What volumes do I work with?
- How precisely do I need to be able to work?
A vacuum pump is characterized by two key parameters: The lowest achievable pressure – also called ultimate vacuum – and the pumping speed. Depending on the respective pressure range, different pump technologies are used for vacuum generation. While the rough vacuum range (~ 1000 mbar down to 1 mbar) can be covered most efficiently with diaphragm pumps, rotary vane pumps are often used to generate fine vacuum (1 mbar down to 10-3 mbar). Specialized screw pumps can be used in both the rough vacuum and fine vacuum range.
Other key differences are chemical resistance to aggressive media and the need for operating fluids such as oil or water. Dry-running pump technologies such as diaphragm or screw pumps offer the advantage that there are no process interruptions due to operating fluid changes and no process contamination caused by oil vapors, for example. Both pump types are also available in chemically resistant versions.
Due to their technology, rotary vane pumps require the use of oil as an operating fluid. The lower chemical resistance should also be noted, as many pump parts are made of metal and can corrode on contact with chemicals. A good alternative in such cases is the chemistry-HYBRID pump from VACUUBRAND. The unique combination of an oil-sealed rotary vane pump and a chemistry diaphragm pump offers better protection against corrosion than a simple rotary vane pump.
The right connection elements and a connection which is as leakage-free as possible are important for achieving the indicated pump specifications. Use a suitable vacuum hose which offers adequate stability and does not become porous. The hose should be as short as possible and have the maximum cross-section possible. The selection of connection elements depends on your pump model and the vacuum connection of the application. We would be happy to advise you in this regard.
Characteristics such as boiling point, risk of corrosion and the quantity of solvent to be evaporated play an important role in the selection and dimensioning of the devices. For example, it makes a decisive difference whether methanol, dimethyl sulphoxide (DMSO) or a multi-component mixture is to be evaporated at a certain temperature, since these substances all have different boiling points. Depending on the area of application, there are therefore different requirements for vacuum generation, measurement and control.
Depending on the application and substances used, it is important that corrosion-resistant pumps are used. This is primarily ensured by the use of chemically resistant plastics in the wetted area (components in contact with the process media like liquids, gas, or air). In addition, when chemicals are mentioned, solvents, i.e. flammable substances, are usually used. Most VACUUBRAND chemistry diaphragm pumps are therefore equipped with an ATEX approval of device category 3 (suitable for zone 2) in the internal, wetted area, so that almost all common solvents can be used in standard laboratory quantities without hesitation.
The ultimate vacuum is the lowest achievable pressure, often specified in millibar (mbar).The lower the value, the stronger, deeper or better the vacuum. The pumping speed is specified in cubic metres per hour [m3/h] or litres per minute [l/min] (1 m3/h ≙ 16,7 l/min). The greater the pumping speed, the faster the pump can evacuate a certain volume.
However, when selecting the right vacuum pump and comparing the pumping speeds of two different pumps, attention should not only be paid to the maximum pumping speed, but in particular to the pumping speed at the actual process pressure. The pumping speed varies with the pressure and decreases in the direction of the ultimate vacuum. The amount of this loss of performance varies from pump type to pump type and also depends, among other things, on design-related details.
At working pressure, there must be sufficient pumping speed to reach and maintain the process pressure. Leaks in the complete system sometimes play a significant role here. Particularly in the process pressure range, the vacuum pump must provide sufficient power to compensate for potential system leakage in addition to the actual process requirements. Otherwise, the maximum achievable ultimate vacuum can deviate significantly from the technical specifications.
It is therefore worthwhile for the user to take a look at the pumping speed curve. This shows the pumping speed as a function of pressure. The shape of this curve makes it easy to recognize how powerful the pump is in the area of the desired process vacuum.
The ultimate vacuum and the pumping speed of a pump depend on the modular connection of the cylinders. Connecting cylinders in parallel increases the pumping speed, while connecting them in series results in a better vacuum – i.e. lower ultimate pressure. VACUUBRAND connects up to four stages in series in its diaphragm pumps and achieves ultimate vacuums between 100 mbar (single-stage) and 0.3 mbar (four-stage). A maximum of two stages are used in the rotary vane pumps, which enable an ultimate vacuum in the range of 10-3 mbar.
The pumping speed of diaphragm pumps is influenced by the parallel connection of the cylinders as well as the number of cylinders and the volume of the pump chamber. In contrast, the pumping speed of rotary vane pumps depends solely on the volume of the pump chamber.
Both individual pumps as well as vacuum network solutions can be used for vacuum supply in the laboratory. The decision between a single-user supply and a network solution depends on various factors. These include, for example, the number of workstations, the applications used or the requirements for vacuum control. Therefore, discussion of the framework conditions and various options with an expert in advance is highly recommended.
In a house network, all workstations in a building are supplied by a large, centralized vacuum pump. However, in-house networks have a number of disadvantages in day-to-day work. Mutual interference and contamination from backflowing gases are difficult to avoid in such systems. This not only disrupts the process sequences, but can also result in safety risks such as the formation of explosive mixtures or the release of infectious material. In addition, such pumps are often oversized because they have to be designed for maximum operation. If it is also taken into account that the pump is in operation around the clock, this results in unnecessarily high investment and energy costs.
The better alternative is therefore local networks like the VACUU·LAN® system from VACUUBRAND. A decentralized vacuum pump only supplies a certain number of workstations in one room. Compared to an individual workstation supply, where each workstation is equipped with a separate vacuum pump, maintenance costs and energy consumption can be reduced in addition to the purchase costs. At the same time, noise emissions and space requirements are lower, as significantly fewer pumps are needed for daily work.
The control of vacuum in the reaction vessel can be achieved in three different ways:
- by manual alteration of the flow rate
- by electronic valve switching
- by rotational speed control
With a simple manual valve alteration of the flow rate, the vacuum can be influenced coarsely without the need for additional aids. However, active and accurate vacuum regulation can only function either electronically via valve switching or via regulation of the rotational motor speed.
In valve switching, also often called on-off control, an electromagnetic valve placed in the suction line between the pump and application is opened and closed. This causes the vacuum to fluctuate between two freely definable tolerance values. This creates a hysteresis.
Diaphragm pumps with speed control of the motor however, enable infinite adjustment of the suction capacity and can achieve the utmost precision in vacuum regulation. Since, in this case, the pump only runs as fast as necessary, the user obtains huge energy savings (up to 90% in comparison to non-regulated systems). Additionally, wear, noise emissions and vibration are significantly reduced.
Modern vacuum controllers like VACUU·SELECT from VACUUBRAND also enable automatic boiling pressure determination. in combination with a variable speed diaphragm pump from VACUUBRAND the VARIO® regulation not only finds the boiling pressure, but also reacts to changes in it thanks to a unique vapor pressure tracking system. Thus, the vacuum is continuously tracked using vapor pressure and then continually optimized to the process demands. In this manner, the results can be achieved in the shortest possible time with just the push of a button, without the need for monitoring and intervention.
Vacuum Pump
Selection Guide
Do you have any
questions?